When it comes to selecting the right pump for specific applications, the material of the pump plays a pivotal role. Two common materials used in the construction of lobe pumps are rubber and metal. But which one is right for you? Let’s dive in.
Introduction to Lobe Pumps
Lobe pumps, a type of rotary lobe pump, are versatile and efficient. They find applications in various industries, from food and beverage to chemical processing. The choice between rubber and metal often depends on the specific requirements of the task.
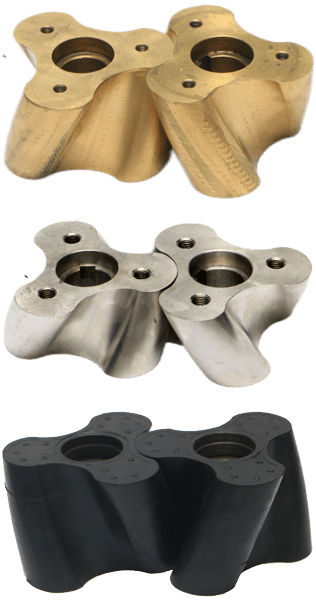
Rubber Lobe Pumps
Rubber lobe pumps are known for their flexibility. The softness of rubber minimizes shear, making them ideal for sensitive fluids.
Advantages:
- Reduced wear and tear.
- Quieter operation due to reduced vibrations.
- Ideal for dirty water and oil and in the soap and detergent industry.
Limitations:
- Susceptibility to chemical degradation.
- Not suitable for very high temperatures.
Metal Lobe Pumps
Constructed from metals like stainless steel, these pumps are durable and can handle high pressures.
Advantages:
- Long lifespan.
- Can handle high-temperature operations.
- Resistant to chemicals, making them suitable for chemical processing.
Limitations:
- Potential corrosion issues.
- Might produce more noise.
Applications and Use Cases
While rubber lobe pumps excel in industries like wastewater treatment, metal lobe pumps are preferred in sectors requiring durability, such as oilfield pumping solutions.
Maintenance and Longevity
Both types require maintenance, but the nature differs. Rubber pumps need checks for wear, while metal pumps should be inspected for rust and corrosion. It’s essential to understand the work principle to ensure proper maintenance.
Conclusion
Choosing between rubber and metal lobe pumps boils down to the application’s specifics. For more insights into different pump types and their applications, explore our knowledge category.
Frequently Asked Questions (FAQs)
How do rubber and metal lobe pumps differ in terms of lifespan?
Metal lobe pumps, due to their robust construction, typically have a longer lifespan compared to rubber lobe pumps. However, with proper maintenance, rubber lobe pumps can also offer extended service life, especially in non-abrasive and non-corrosive environments.
Can rubber lobe pumps handle abrasive materials?
While rubber lobe pumps can handle some level of abrasiveness due to their flexibility, they might wear out faster than metal pumps in highly abrasive conditions. It’s essential to consider the nature of the fluid and suspended solids when choosing the pump material.
Are metal lobe pumps more expensive than rubber lobe pumps?
The cost can vary based on the specific metal used, design, and brand. However, metal lobe pumps, especially those made from specialized alloys, might be more expensive initially. It’s crucial to consider not just the initial cost but also operational and maintenance costs over time.
Which pump type is more energy-efficient?
Energy efficiency can vary based on the design, motor, and application. However, both rubber and metal lobe pumps are designed to be efficient. For specific energy consumption details, it’s best to refer to the manufacturer’s specifications.
How often should I maintain my lobe pump?
Maintenance frequency depends on the material, usage, and the nature of the fluid being pumped. Regular inspections are recommended for both types. For a detailed maintenance guide, check our maintenance category.